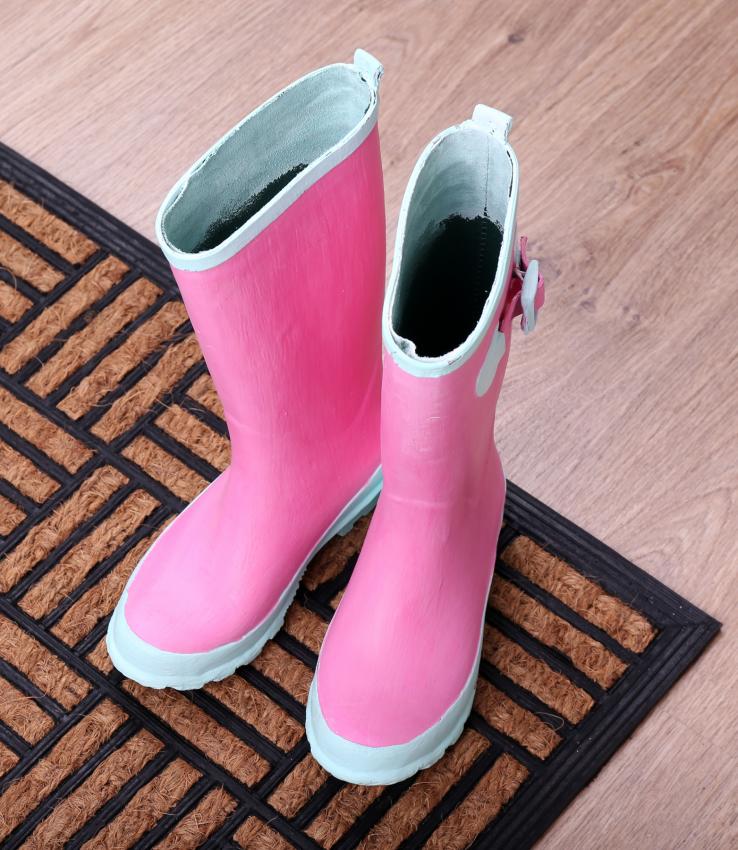
UK-based Gumdrop Ltd. recycles pre- and post-consumer waste chewing gum into a raw material called Gum-Tec for thermoplastic elastomers (TPEs). The company asked Teknor Apex to apply its expertise as a leading custom compounder, especially in TPEs, to develop and produce compounds from this material. The challenge was to come up with formulation and manufacturing techniques for a new type of raw material, to produce commercial-scale quantities of compounds that consistently meet the requirements of specific applications. Those requirements include optimized elasticity, compression set, tensile properties, and other mechanical properties, plus processability. The new TPE compounds contain up to 30% of the chewing gum-based raw material. They can be formulated for either glossy or matte finishes, readily accept colors, and are recyclable. Commercial applications for the Gum-Tec TPE compounds include Wellington boots, caster wheels, automotive bumpers and floor mats, shoe soles, window gaskets, and wristwatch straps. (Source: Teknor Apex)
As bio-based and renewable plastics become more common, and more plentiful, the raw materials used for feedstock are also getting more varied. This slideshow includes a new thermoplastic elastomer (TPE ) made from pre- and post-consumer waste chewing gum, and a new line of black masterbatches that contain 100% recycled post-consumer tires.
While many, many R &D attempts have been made to harness overly plentiful carbon dioxide for chemical feedstocks, few have made it all the way to commercialization on the industrial scale. After many years of intensive effort, chemical giant Covestro has achieved that goal, as we tell you in the following slides. Additives that aid recycling are also becoming more important, and we feature two of those. We also tell you about a first: BASF’s new ecovio EA is the first-ever expandable, closed-cell foam material that’s biobased and also certified compostable, making it a green replacement for expanded polystyrene (EPS).
[Source:-Design News]